導入の背景
短納期を強みとするからこそ「リアルタイムの工程管理」が重要
東京・品川区に本拠を置くアース アテンドは、プラスチック、ゴム製品、カーボン素材の製造加工会社です。1973年、配管の継ぎ手に用いる工業用ガスケット・パッキングの製造会社として出発し、フッ素樹脂の精密加工技術の蓄積を活かして、ゴム部品やカーボン素材の精密切削加工にも進出しました。同社が作る高精度な部品は、自動車、半導体製造装置、プラント配管、食品工業、航空宇宙、バイオテクノロジーなど、幅広い分野で利用されています。
「当社は、『1個』からの加工にも応じて、最短で受注当日の出荷をしています。さらに、当社では作っていないチタンなどの部品も一括受注し、協力会社で製造加工したものを取りまとめてトータル納品もしています。お客様の必要なものを望む形で即座に提供する精密樹脂加工技術の集団であると同時に、商社の機能も果たせるのです」と、取締役 COO(Chief Operating Officer:最高執行責任者)の志村英雄氏は紹介します。
同社の小回りのきく迅速対応には定評があり、「今日受注し、今日作って、今日出荷する」という当日出荷品は1日平均100件にものぼります。
しかし、短納期を極限まで追求しているだけに、顧客からは「今朝頼んだものは、どこまで進んでいるか」「何時に取りに行けばいいか」などの問い合わせが頻繁に寄せられます。製造の主力を担う小山工場は、本社から徒歩15分程度のすぐ近くにありますが、これまでは、本社と小山工場間でひっきりなしに電話のやりとりをしていました。
「問い合わせのきた案件が、受注、製造、検査、出荷のどのプロセスにあるのか、すぐにわかるようにしたい。短納期を強みとする当社にとって、『リアルタイムの工程管理』は、年来の経営課題でした」と志村氏は言います。

取締役 COO 志村英雄 氏
導入のポイント
シンプルな工程管理と バーコードを利用したきめ細かな工程管理を併用
2004年、販売管理システムを刷新するにあたり、アース アテンドは、「安く、信頼性高く、使いやすいパッケージで、販売管理と工程管理を統合できるもの」(志村氏)を探しました。
「5社ぐらいに要件を説明して提案してもらいましたが、当社の要望を現実の形にしてくれそうだったのが、楽商シリーズの『加工外注マイスター』」だったのです」と志村氏。
まず楽商の販売管理は、受注から、発注、仕入、売上、売掛買掛まで一元管理でき、「今日、今の時刻までにいくら受注したか」が、画面を見るだけでわかります。
「これは画期的でした。受注しているが売上になっていない『受注残』がリアルタイムに把握でき、今週の仕事がいまどの程度混んでいるのかもわかりますから、経営判断がやりやすくなり、営業の動き方も機敏に変えられるようになりました」と志村氏は言います。
また、マスタ登録しなくても受注入力ができるため、100個100仕様の即日出荷にも柔軟に対応できます。社内および協力会社への加工依頼や資材発注が受注入力と同時に行えるなど、製造加工業の業務に密着した機能を網羅しているため、販売管理はほぼ標準形のままで導入しました。
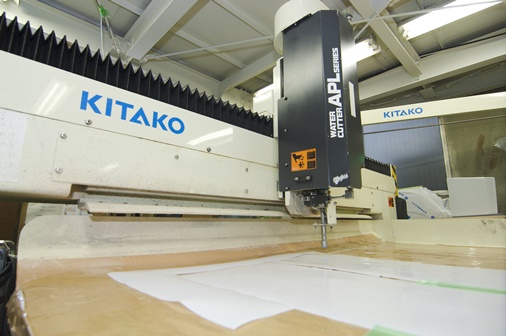
製造の主力を担う小山工場
販売管理システムをカスタマイズして工程管理まで実現
さらに2011年、導入当初のねらい通り、使用中の楽商に工程管理を追加開発することにしました。
「工程管理の単体パッケージで、当社の要望に合致するものはみつかりませんでした。当社がやりたいのは、部品1個を作る工程をリアルタイムに見えるようにすること。即日出荷品の管理プロセスは、製造開始、製造終了、検査終了の3プロセスで十分です。しかし単体の工程管理システムは、数多くの工程を経て大量製造する大企業向きのものであり、当社では使わない機能が山ほどあって、値段が非常に高かった」と志村氏は語ります。
楽商のカスタマイズ開発は順調に進み、2012年12月、販売管理と連動する工程管理システムが稼働を開始しました。
工場では大型ディスプレイで進行状況をリアルタイム表示
小山工場には大型ディプレイが設置され、即日出荷品の製造進行状況が映し出されます。
ここに表示されるのは、製造開始と検査終了の2プロセスだけ。進行状況は15秒毎に更新され、検査終了して出荷に回された案件は赤色表示に変わります。スクロールも3秒単位で自動的に行われ、短い時間で複数ページの最後まで見られます。国際空港のフライト情報表示システムを思わせる風景です。
「責任者はもちろん、製造担当者も、検査担当者も、いつも大型ディスプレイをちらちら見ています。今日終えなければならない仕事が予定どおりに進んでいなければ、使う機械や人の配置をすぐに工夫します。急ぎの注文が入ったときは上位に表示されますから、作業の優先順位に変化があったことも確認できるのです」と志村氏は説明します。
本社/小山工場間は、インターネットVPNでネットワーク構築されましたから、大型ディスプレイの表示内容は本社でも見ることができます。顧客からの納期問い合わせには、掛かってきた電話を一旦切ることなく、そのまま回答できるようになりました。
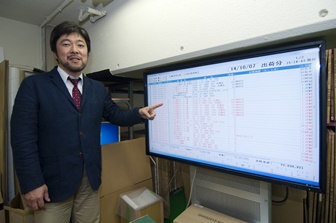
小山工場の大型ディプレイ
バーコード導入できめ細かいコスト管理と品質管理
翌2013年、製造現場での入力の手間を増やすことなしに、工程の進行状況をよりきめ細かく把握するために、バーコードを導入しました。現在バーコードを用いているのは、即日出荷品以外の商品で、製造工程数の多い特定顧客の特定商品です。
対象商品は、受注入力し、工場で製造指示書を印刷した時点で、自動的にバーコードが印刷されています。これをバーコードリーダでピッと読み取ることから、工場での製造工程が始まります。管理する工程は最大7つです。
アース アテンドでは、本社事務所に1台、本社工場に3台、合計4台のバーコードリーダを設置。製造完了時には、作業にかかった時間も手入力して、精度の高いコスト管理をするようになりました。また、どの機械で、誰が、何時間かかったかを統計分析することで、品質管理にも役立てています。
「バーコードリーダーは、ハンディターミナルの10分の1程度の値段で安価です。工程管理単体ソフトとハンディターミナルの組み合わせではなく、楽商とバーコードリーダの組み合わせによって、管理項目の多い工程管理まで、非常に低コストで実現することができました」と志村氏は評価します。
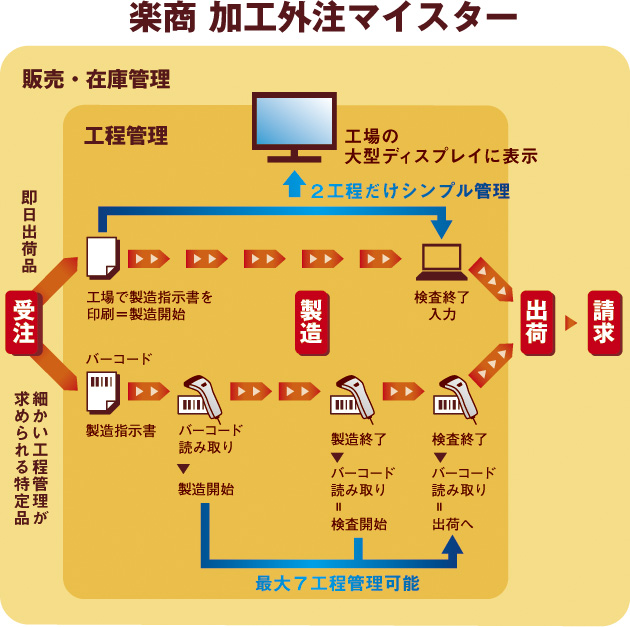
導入の効果
単体工程管理システムの4分の1のコストでやりたいことを網羅
即日出荷品のリアルタイムな工程管理を、シンプル、スピーディにやりたい。製造工程数の多い特定商品は、バーコードを使ってきめ細かく工程管理をしたい。
アース アテンドの年来の課題は、楽商をカスタマイズすることで、低コストに実現することができました。
「単体の工程管理システムに比べて4分の1の投資で、やりたいことをすべて網羅できました」と志村氏。
しかも楽商は、受注から、製造、出荷を経て、請求・売掛買掛まで、データを一元管理しています。販売管理/工程管理間で、顧客マスタ、商品マスタも一本化できて効率的です。
本社でも工場でも、同じ情報をリアルタイムに見られるようになって、本社から工場への電話問い合わせは不要になりました。電話で作業を中断されることがなくなり、本社/工場ともに業務効率があがっています。納期回答が早くなったと、顧客からも喜ばれています。
今後は、バーコード管理の全商品への拡大、タブレット端末を使ったモバイル利用、製造進行状況を顧客がWebで確認できるようにするなど、新たな課題に取り組んでいきます。管理項目にしきい値を設定しておき、一定期間動いていない機械、動いていない案件などをシステム側でチェックして通知してくる体制にしたいとも考えています。
「日々の業務に不可欠なシステムは、止まらないことが最も重要です。その点、楽商は安定して稼働しており、安心して長く使えます。しかもJSTは、当社のシステムを同じ担当者がずっと担当してくれています。これも業務を支えるシステムにとって、重要な要素ですね」と志村氏はにこやかに語りました。
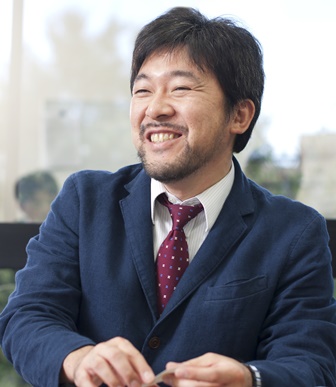
笑顔で対応して頂いた志村氏
アース アテンド株式会社 様
代表者:代表取締役 志村武雄 / 業種:プラスチック製品製造加工業
事業内容:ガスケット・パッキング・フッ素樹脂加工・販売
URL:http://www.earth-attend.co.jp/
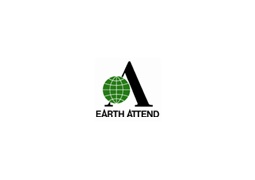
- どのサービスが一番適している?
- 課題がまだまとまっていない。
- こういう事例はある?
- 見積もりだけでもいい?